リチウムイオン電池の製造工程におけるレーザの採用事例
2024.4.2 2024.4.2
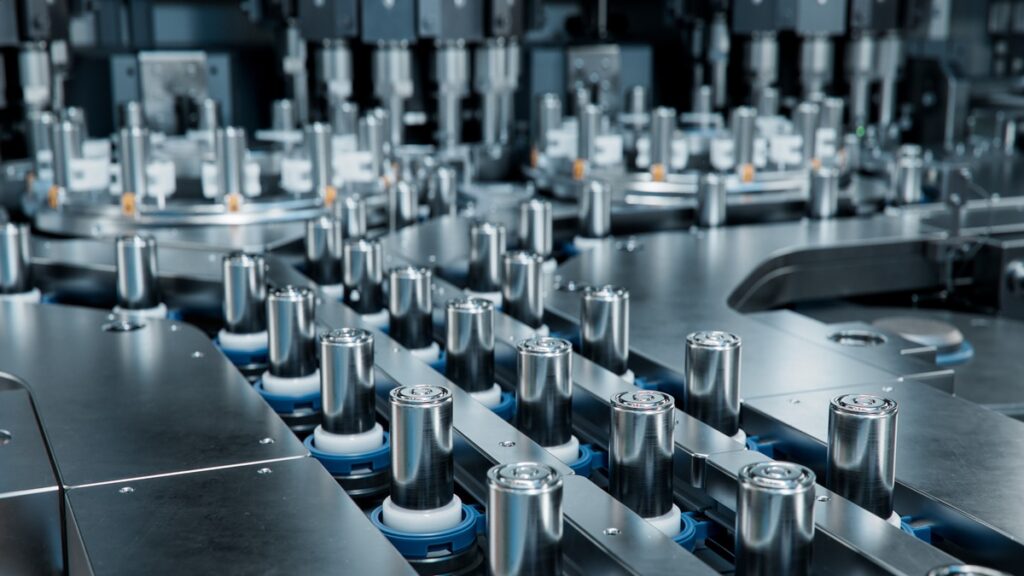
リチウムイオン電池製造では、電極の切断、積層、溶接、封止といった工程でレーザを活用できます。しかし、レーザの採用にどのようなメリットがあるかわからない方も多いのではないでしょうか。
この記事では、リチウムイオン電池製造におけるレーザの採用事例やメリットなどについて解説します。電池製造でレーザの採用を考えている方に役立つ情報をご紹介しますので、ぜひ参考にしてください。
リチウムイオン電池の製造工程
リチウムイオン電池は以下の工程で製造されます。
- 原反工程
- 組立工程
- 仕上げ工程
- 検査工程
原反では、電極を作ります。正極の場合はニッケルやコバルト、負極の場合は炭素系材料といった活物質と有機溶剤などを混ぜ合わせるのが基本です。ペースト状にした材料を、アルミニウム箔を始めとした金属箔に塗布し乾燥させたあとにプレスします。
組立では、プレスした電極を寸法に合わせて切断し、正極と負極の間に絶縁用セパレータ―を挟んだあと巻き取ります。巻き取った電極をケース(セル)に挿入して電池を組立、電解液を注入してから蓋を気密封止すれば外装の組立は完了です。
仕上げでは、繰り返し充放電を行って電池を活性化させ、内部に生じたガスを抜きます。検査では、できあがった電池の性能や容量などの検査を行い、問題がなければ全工程の完了です。
リチウムイオン電池の製造にレーザが用いられる理由
リチウムイオン電池の製造では、レーザを使用するのがおすすめです。ここでは、レーザを用いるメリットについて詳しく見ていきましょう。
【レーザが用いられる理由】
- 精密な加工ができる
- 作業工程を削減できる
- さまざまな形状に対応できる
- 加工できる素材の範囲が広い
レーザは、集めた光をピンポイントで素材に当てるため、細かく精密な加工が可能です。刃物を使った場合のように粉塵が発生する恐れがなく、カエリやバリも抑えられます。ひび割れや歪みも生じにくいため綺麗な切断面に仕上がり、高い品質を保てるのがレーザのメリットです。
また、レーザは従来の金属加工のように金型を必要とせず、事前に用意したプログラムをもとに加工を進められます。そのため、金型の製造やセッティング、交換、メンテナンスといった工程を削減できるのもレーザの利点です。刃物と比べてカエリやバリを処理する時間も削減でき、作業の効率化につなげられます。 ほかには、構築したプログラム次第でさまざまな形状に対応できるのもレーザの魅力です。切断加工はもちろんのこと、彫刻や穴あけなどバリエーション豊かな加工ができます。
近年需要が高まるリチウムイオン電池製造では、薄い金属をなるべく速く加工する技術が求められています。精密な加工ができ、作業効率を上げられるなどのメリットを備えたレーザなら、リチウムイオン電池製造に役立てられるでしょう。
リチウムイオン電池の製造におけるレーザの使用例
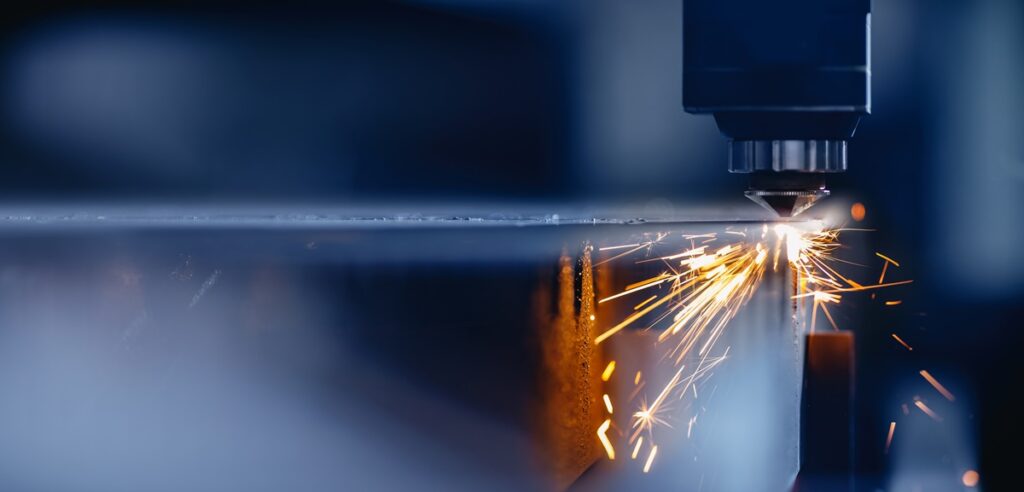
リチウムイオン電池の製造工程では、以下の作業でレーザが使われています。ここでは、各作業について詳しく確認していきましょう。
【レーザが用いられる製造工程】
- 電極の切断
- 電極の積層
- 電極の溶接
- 電池の封止
電極の切断
電極の切断とは、乾燥させてプレスした電極を寸法に合わせてカットする工程です。レーザを使うことで、活物質層や金属箔に対する熱影響を抑えられるのに加え、切り口に生じやすい金属箔の露出や金属ダマを低減できます。活物質の有無を問わず、シャープかつスピーディーな切断ができるのもレーザのメリットです。
電極の積層
電極の積層は、正極・負極・セパレータを交互に積層する工程です。近年は、銅に対する高い光吸収率を備え、安定的に入熱の制御ができる青色レーザの注目度が高まっています。
電極の溶接
電極の溶接は、積層された電極にタブリード(電池から電気を取り出す端子)を溶接する工程です。レーザを使えば、溶接部内部の隙間を抑え、質の高い積層溶接を叶えられます。また、内部や表面に溶接欠陥が生じるのを防げるのもレーザのメリットです。ビームプロファイル制御技術を搭載したレーザであれば、積載溶接でも貫通性と安定性を両立させられます。
電池の封止
電池の封止は、電解液を注入した電池を隙間なく密閉する工程です。封止におけるアルミニウムの重ね溶接では、融点の低さが要因となって溶接部内部に隙間が生じやすくなります。ビームプロファイル制御とレーザを組み合わせれば、内部の隙間を防ぎ、安定した溶接が可能になるのも大きなメリットです。
今期待されているリチウムイオン電池の技術開発について
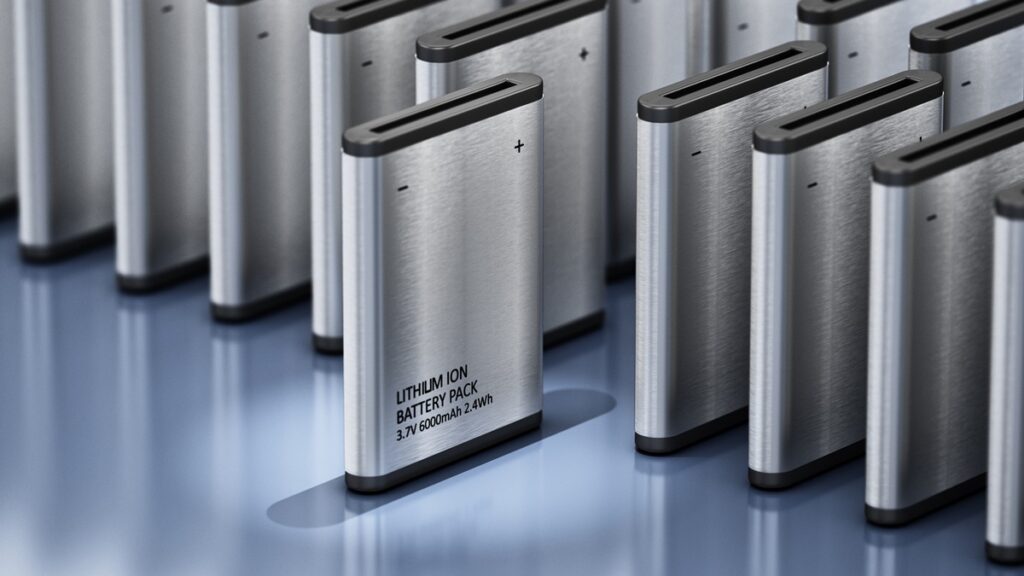
近年、国によってはリチウムイオン電池の技術開発が推進されています。今後期待される電池の種類として挙げられるのが、全固体リチウムイオン電池とラミネート(パウチ)形リチウムイオン電池です。
全固体リチウムイオン電池は、温度変化に強く、急速充電でも発熱のリスクが少ないという性質を持ちます。ラミネート(パウチ)形リチウムイオン電池は、外装にラミネートフィルムを使用しているため、軽くて薄いのに加え、温度上昇を抑えられるのが特徴です。ここでは、各電池についてさらに詳しく見ていきましょう。
全固定リチウムイオン電池
現在の蓄電池は液体リチウムイオン電池が主流ですが、今後は次世代蓄電池として全固体リチウムイオン電池の台頭が期待されています。
全固体リチウムイオン電池とは、電流を生じさせるための電解質を固体にした電池のことであり、液体電解質より高い性能を備えています。2020年代後半以降にはEV市場で取り入れられる可能性もあるため、注目しておきたい電池の1つです。
【全固体リチウムイオン電池の特徴】
- 可燃性の電解液による発火・液漏れの恐れがなくなり安全性が向上する
- 安定性が高く、幅広い温度に対応できるため、温度変化による問題が生じにくい
- 発熱のリスクが低く、安全に急速充電ができる
- 液体の電解質と比べて劣化しにくく、寿命が長い
- 液漏れの心配がなく、設計の自由度が高い
従来、全固体リチウムイオン電池の研究開発は日本が各国をリードしてきましたが、近年は他国の追い上げが目覚ましく、特に中国が存在感を増してきました。そのため、日本でも全固体リチウムイオン電池のスピーディーな開発が求められています。
ラミネート(パウチ)形リチウムイオン電池
ラミネート(パウチ)形リチウムイオン電池とは、積層した電極を軽量なラミネートフィルムで包み込んだ電池のことです。
【ラミネート(パウチ)形リチウムイオン電池の特徴】
- 金属缶を使った従来の電池と比べ、薄くて軽量
- 広い表面積によって高い放熱性を備え、充放電による温度上昇を抑えられる
- 金属缶を制作する必要がないため、金型製作や調整にかかる作業工程を削減できる
金属缶を使った円筒形や角形のリチウムイオン電池は頑丈な性質を持つ一方で、重量は重くなります。ラミネート形であれば、従来よりも軽くて薄い電池の製造が可能。また、コストパフォーマンスと安全性に優れたマンガン酸リチウムを使用しているため、コストダウンにもつなげられます。
近年は、ハイブリッドカーや電気自動車の分野でも、軽量かつ安全性の高いラミネート形リチウムイオン電池が注目を集めています。カーボンニュートラルを見据え、今後もハイブリッドカーや電気自動車のニーズは高まってくると考えられるため、ラミネート形リチウムイオン電池の注目度もさらに高まるでしょう。今後も新製法の開発や、さらなるコストダウンに期待されています。
まとめ
電気自動車などの普及により、リチウムイオン電池は今後さらに需要が高まると考えられています。微細かつ効率的な加工が可能なレーザは、電池製造において大きな役割を担う可能性が高いでしょう。
伯東では、レーザ機器専任のチームがお客様のニーズを聞き取り、レーザ発振器単体から加工機一式まで幅広く提供いたします。レーザの活用についてご検討の場合は、ぜひ伯東にご相談ください。
よく見られている記事
関連するソリューション
-
微細穴あけ加工
Novanta社 ARGESブランドの5Dガルバノスキャナと超短パルスレーザ発振器を組み合わせたレーザシステムで、金属、ガラス、樹脂、セラミックス、シリコンなど多様な素材の微細穴あけ加工に対応。自社アプリケーションラボで […]
-
レーザ加工画像処理システム
レーザ加工画像処理システムとは、加工前に対象物を撮像することで、加工位置を高精度に制御できるシステムです。
-
AOD導入による超高速レーザ加工システム
レーザ加工にAODを導入することで、従来のガルバノスキャナの10倍以上の超高速加工が可能になります。
-
アプリケーションラボ
アプリケーションラボは、お客様が各種レーザ機器、加工機を導入する際に利用できる施設です。ここでは、レーザ発振器やガルバノスキャナヘッドなどの選定やこれらを使用した加工条件の検証を事前に行うことができます。実際の機器を見な […]
-
レーザタブノッチングシステム
伯東はレーザノッチングシステムを日本で初めて市場導入したパイオニア企業であり、電極タブ加工に最適なシステムを提供できます。
-
レーザ溶着
伯東はレーザ溶着に必要な4つの主要システムをワンパッケージ化した溶着システムを提供しております。